The company formerly known as AxonVR, which has raised more than $5 million in venture capital, is rebranding to HaptX, and revealing a feature prototype of a VR glove which uses micro-pneumatics for detailed haptics and force feedback to the fingers. After trying the prototype for myself, I came away impressed with the tech. The company’s next challenge is to turn the prototype into something sleeker, smaller, and far more practical.
Fitting Procedure
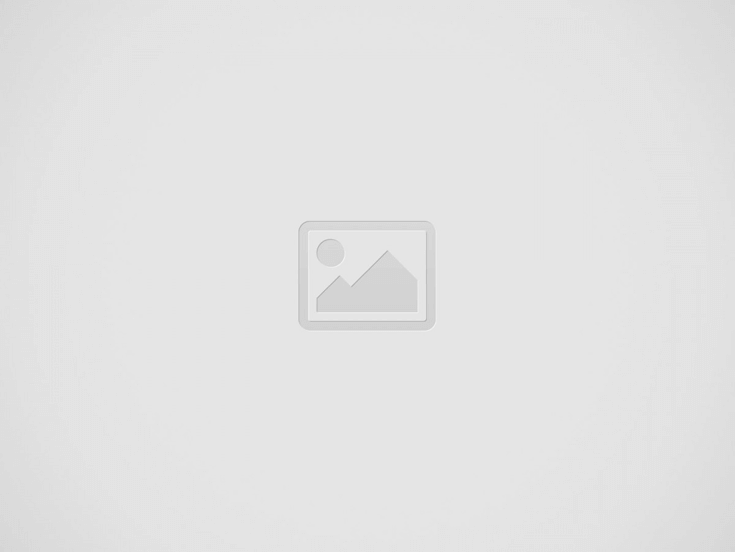
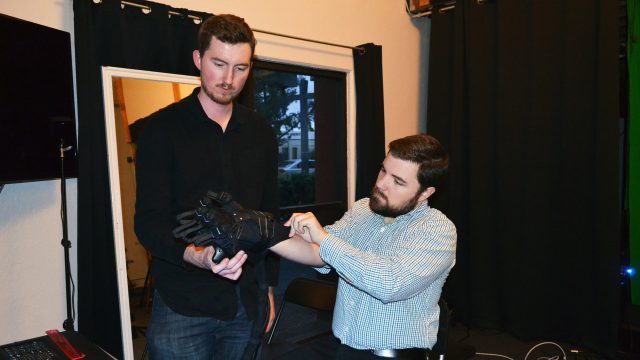
Meeting with HaptX co-founder Jake Rubin in Silicon Valley earlier this month, I got to try the latest prototype of the company’s wild-looking haptic VR glove—a monstrous piece of equipment hooked up to some massive cabling. Putting it on—with the help of two people by my sides—I felt like I was preparing for a medical procedure, as the pair showed me how to carefully guide my fingers into the right places, pull out some fabric slack, and then tighten the glove to my hand with a ratcheting mechanism to ensure a snug fit. But the point of this prototype is not about size and fit, it’s all about function. And function it did—the haptics and force feedback were the most responsive and detailed I’ve tried to date, in part thanks to the glove’s micro-pneumatics.
Micro-pneumatics
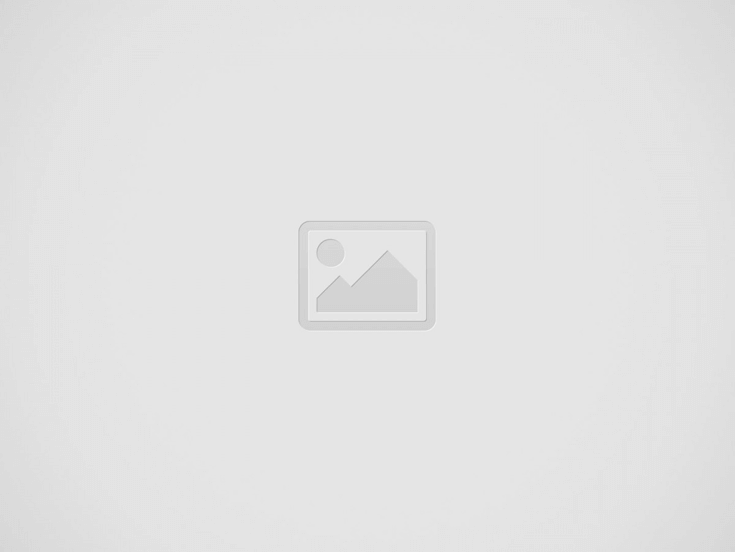
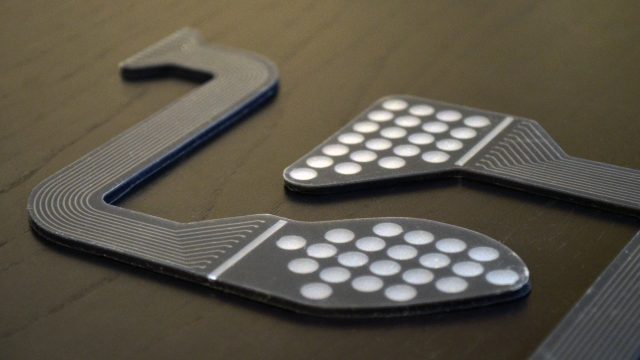
The HaptX gloves is based on innovative micro-pneumatic technology. The company has developed a method for essentially producing thin, bendable fabrics which are manufactured with a series of tiny air pipes along their length which eventually terminate in small inflatable circles which act as “haptic pixels,” according to Jake Rubin, one of the company’s two co-founders and its CEO. The inflatable circles, just a few millimeters across, are aligned into grids; by precisely controlling when and which haptic pixels to inflate, a convincing sensation can be created, simulating the feeling of an insect crawling along your finger or a marble rolling around in the palm of your hand.
The glove also features force feedback: the ability to restrict the movement of your fingers to simulate holding objects. This too is based on the company’s micro-pneumatic technology, which Rubin explained works by inflating stoppers along the joints of your fingers to restrict their movement. The effect is that when you reach out to grab an object, say, a baseball, your fingers stop right where they should be coming in contact with the baseball.
Both effects were impressively responsive and quite convincing. I’ve tried a few other similar systems, but the haptics from the HaptX glove blew the others away. The glove puts the haptic material across the palm of your hand and on the tips of your fingers—totaling some 100 individual haptic pixels—allowing you to feel a finely detailed sensation of pressure in all those places. The range of tactile sensations was ultimately surprising; revealed to me when I was thrown in to the company’s farm-themed menagerie of tactile examples.
Feeling the Farm
Rubin walked me through the demo experience, built using an SDK of HaptX’s design, which he says is largely created by leveraging Unreal Engine’s physics system to tell the glove when and where to apply haptic effects and when and how to engage the force feedback.
With the glove on my right hand, and wearing an HTC Vive headset, I was looking down at a miniature barnyard with some little sunflowers off to the right and a tiny patch of wheat in front of a barn. Rubin encouraged me to start poking and prodding at the scene. Each of the glove’s fingers is tracked by a proprietary magnetic tracking system which Rubin claims is capable of sub-millimeter precision. Indeed it worked well.
As I reached out with my index finger to gently touch the leaves on the side of the sunflower, I could feel pressure against my finger that quickly and closely followed the visuals, making it easy to connect the feeling with the image.
Next to the sunflowers was a little grey storm cloud, and when I poked it, pea-sized raindrops began falling from within. Stretching out my palm to catch them, I felt a convincing pitter-patter of pressure right on my palm. A similarly convincing moment came when I brushed my palm across the tops of the tiny wheat plants.
Eventually a baseball-sized tractor came rolling out of the barn. When I went to pick it up like a little toy, my fingers stuck in place—seemingly right against the virtual tractors surface—and wouldn’t budge. It was a convincing effect, especially combined with the haptics putting pressure on the tips of my fingers as though I was holding something. Although there’s no way for the gloves to simulate the weight of the object, making it feel like it was at least real, as far as the volume that it takes up, is a big step up. ‘Mock grabbing’ items with controller-less VR hand input feels really unnatural, but the quality of this force feedback remedied that with ease.
There was more to do and see in the demo, including some tiny critters that came out of the barn to dance around on my palm so that I could feel their little steps (including the eight legs of a spider, which Rubin tells me is the most contested part of the demo). In the end though, the whole ordeal provided me with a new benchmark for small-scale haptics in VR.
Continued on Page 2: Enterprise First »
Page: 1 2